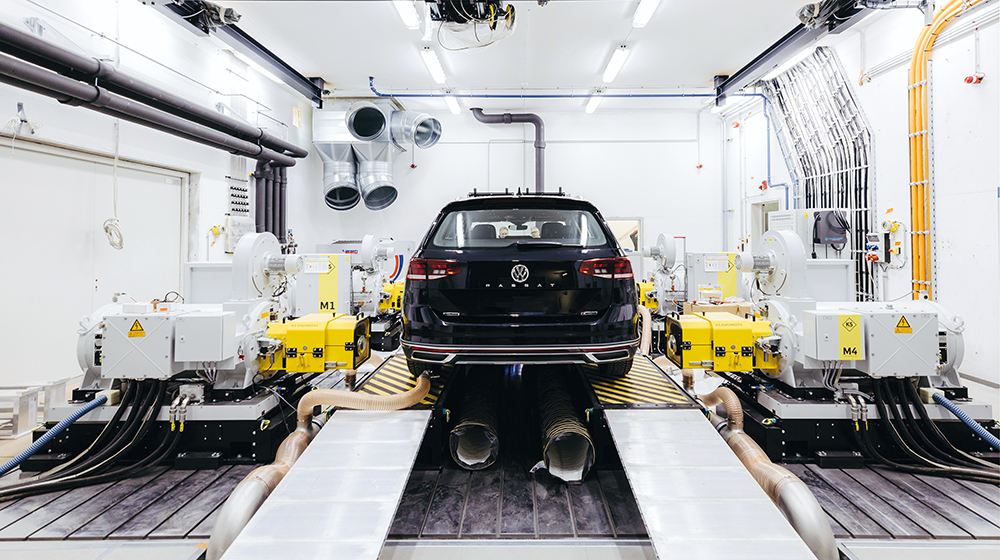
An automobile manufacturer develops a sustainable drive system. He builds the prototype into a vehicle, tests it, adjusts a wide range of parameters, rebuilds the drive system, develops the components a bit more, builds a new prototype, and so on... He is learning by doing. But learning by doing takes time. And climate change and the energy crisis are not leaving much time for the mobility transition. Since 2023 in the Center for Method Development (CMD) at the Ostfalen Technology Park near Magdeburg, a new Research Center for Method Development will become operational. Engines and batteries and their components will no longer be tested on the road here, but instead in the virtual sphere, a process that is considerably quicker and more cost effective.
Until now, the main route to the mobility transition has been to use the road as a test track. But thanks to the opportunities presented by the digital age, this can now be relocated to the virtual space. Therefore, the Otto von Guericke University Magdeburg laid the foundation stone for a Center for Method Development (CMD) in Ostfalen Technology Park in nearby Barleben. The methods concerned are virtual methods for significantly shortening the development time of sustainable forms of drive system. “We will replicate a real vehicle one-to-one in the form of a digital twin in which the components for alternative drive systems will be tested,” says the University’s President, Professor Dr.-Ing. Jens Strackeljan, a mechanical engineer by training. The President was previously Professor of Technical Dynamics in the Institute of Mechanical Engineering at the University of Magdeburg before being appointed to the top job in 2012.
Aerial view of the Center for Method Development at the University of Magdeburg (Photo: Jana Dünnhaupt / University of Magdeburg)
It has been just as long since an open laboratory infrastructure has been considered in the automotive sector. At any rate, as Strackeljan highlights, there are 26,000 employees from Saxony-Anhalt in the automotive supply industries and these small and medium-sized enterprises mostly cannot afford their own state-of-the-art facilities for research and development. But on the university campus in Magdeburg, “automotive” is established as a key area for research and transfer as there are many large automobile manufacturers and their suppliers with a presence in the surrounding area. “The innovations generated at the university must be used in industrial applications,” stresses Jens Strackeljan.
It is this very objective that Dr. Jürgen Ude, State Secretary for Structural Transformation and Major Industrial Facilities in Saxony Anhalt, is pursuing. The qualified Materials Engineer has been associated with automotive engineering for decades - from the management of the MAHREG Automotive Cluster and the inception of the Institute of Automotive Expertise (IKAM) at the University of Magdeburg to the leadership of the Innovation and Start-Up Center in Barleben. “The idea of establishing a Center for Method Development, in order to reduce testing times, has been around since 2015,” says Jürgen Ude, going on to add that initially the emphasis lay on the internal combustion engine. In keeping with the current challenges of sustainability, climate neutrality and the requirements of autonomously driven vehicles, the areas under research themselves are now also being put to the test. In itself each task is already demanding. The University President and the State Secretary agree that to overcome these challenges simultaneously, new, efficient development methods will be required.
One man who is familiar with road testing from his professional experience in the automotive industry is Professor Dr. Hermann Rottengruber. Before taking over the leadership of the Department of Energy Conversion Systems for Mobile Applications at the University of Magdeburg, he was employed at BMW in Munich looking at novel drive systems for diesel engines. As long ago as the 1990s, he was involved in researching green hydrogen as an alternative fuel and in 1999 wrote his doctoral thesis on the performance and exhaust characteristics of a hydrogen/diesel engine. Subsequently he was involved in the development of the BMW Hydrogen 7, the first mass-produced hydrogen car. At the time, in Germany the necessary hydrogen infrastructure was nowhere near being in place. Rottengruber emphasizes that implementing it is still one of the mammoth tasks for the energy transition today. The development of hydrogen drives and engines especially for commercial vehicles is, in contrast, well advanced. Since 2019, Hermann Rottengruber has led the Institute of Mobile Systems (IMS) at Magdeburg University. Research into modern drive systems, he says, follows a holistic approach here - from the use of synthetic fuels and electric drive systems through to hydrogen. “With the new Center for Method Development, for the first time the University of Magdeburg has a state-of-the-art, high-performance testing environment in which we can really get to grips with hydrogen drive systems and fuel cells,” says Hermann Rottengruber.
Prof. Dr. Hermann Rottengruber (Photo: Jana Dünnhaupt / University of Magdeburg)
Dr. Martin Schünemann is also involved in the design of the CMD research center. Since commencing his studies at Otto von Guericke University Magdeburg in 2004, the mechatronics engineer has had an interest in electromobility and has carried out many vehicle tests. One insight he has gained is that for example for large goods vehicles with heavy loads or for transports that have to cover long distances, for example, the pure electric engine is not an efficient converter of energy. At this point, Martin Schünemann mentions hybrid vehicles, which have multiple energy converters in a single system. “A hybrid drive is, however, only efficient if all components work together well,” he clarifies. “The electric engine, combustion engine or fuel cell and the battery have to be interconnected during operation in such a way that they use as little energy as possible. Whether that works well or not can only be tested in an interconnected system.”
Martin Schünemann is involved with other colleagues from the University of Magdeburg in coordinating the interaction of the individual test facilities in the CMD. Initially there will be eleven test facilities, which will be concerned with engine and engine-transmission testing,
- the testing of short-stack fuel cell systems of different performance categories,
- with high torque and high-rev engines,
- climatic chamber and acoustic measurement of electric engines,
- the testing of whole battery systems and with performance electronics, as well as,
- testing the resistance and corrosion of contacts.
- And there will be a battery simulator.
These individual testing facilities can be switched together synchronously and simulate a real car, in which the interaction between the individual components of the engine and battery are tested. For this purpose, real driving scenarios are simulated, with an external temperature of 40 degrees being one example that Schünemann gives. Whether or not new drives can cope with such high temperatures is an important question in light of climate change.
Dr. Martin Schünemann (Photo: Jana Dünnhaupt / University of Magdeburg)
“If the road tests are transferred to virtual testing facilities, development times can be reduced by a factor of two to three and the construction of prototypes can be reduced, which also saves time and money. And since nowadays developments no longer take place in a linear fashion, they can be tested in advance due to the possibility of advance simulation,” stresses Hermann Rottengruber.
Materials research also benefits from this. On the real road, a car is literally exposed to wind and weather - and other completely different mechanical stresses. Dr. Thorsten Halle, Dean of the Faculty of Mechanical Engineering and Professor of Metallic Materials at the University of Magdeburg monitors their mechanical stability; that is the resistance of materials, compounds and components against deformation and breakage. “An electric engine, for example, consists of other drive components, meaning that other materials are built in. This produces new properties, different force transmissions within the integrated system,” the materials scientist explains, going on to add that in the Research Center for Method Development the drive components are subjected to mechanical stresses both individually and as they interact. Joins and connections must hold within a system that is moving on the road - including in wind or bad weather. The latter might entail rain, snow and road salt. “Corrosion is an important topic for us. In the CMD it is now possible for us to test whole components with regard to corrosion and not just the individual materials as previously,” explains the Professor.
At the end of the virtual test track there is a hydrogen-capable road-to-rig whole vehicle testing facility on which the entire digital twin of the actual car can be tested. If the real car were not to pass the road test, that would be a bitter setback, as Herman Rottengruber knows from his previous professional experience. If the virtual car does not work, the errors can first of all be found more quickly on the computer and having to produce an expensive additional prototype can be avoided.
Preparation of the examinee for the planned tests in the CMD by Prof. Hermann Rottengruber, Torsten Winkler, Frank Wieprecht and Marian Schröder (Photo: Hannah Theile / University of Magdeburg)
This is where the art of engineering meets AI, combining in exemplary fashion. The University President, Jens Strackeljan, highlights the excellent interdisciplinary collaboration between the departments of Mechanical Engineering, Electrical Engineering, Natural Science and Computer Science. In the context of research projects he believes there are many topics for student theses and dissertations in this field.
As the first partner, MAN Truck & Bus Deutschland supports the University of Magdeburg with a diesel engine. The individual developmental stages of converting it to run on hydrogen will be tested here. State Secretary Jürgen Ude attests to the fact that “with the appeal of excellence, the CMD is drawing attention to the highly effective automotive research in Saxony-Anhalt and increasing the attractiveness of our industrial and scientific center.”
“The CMD is also creating an attractive environment for students who want to play an active role in the energy transition,” adds University President Jens Strackeljan, highlighting the fact that methods for monitoring the testing facilities are also being developed. These could then be transferred to other areas such as the monitoring of wind farms.
Guericke facts
-
Hydrogen is an important building block in the defossilization of road transport
-
A 40 tonne battery-electric LGV requires between 350 and 500 KW of charging capacity, which corresponds to approx. 30 cars at fast-charging stations or the power that an inter-city train at full acceleration draws from the power grid.
-
With hydrogen as a molecular energy store, the energy stores of heavy goods vehicles can be charged considerably more quickly and efficiently than batteries from the power grid. Here the molecular energy store of hydrogen is superior to the battery as an electrical energy store.