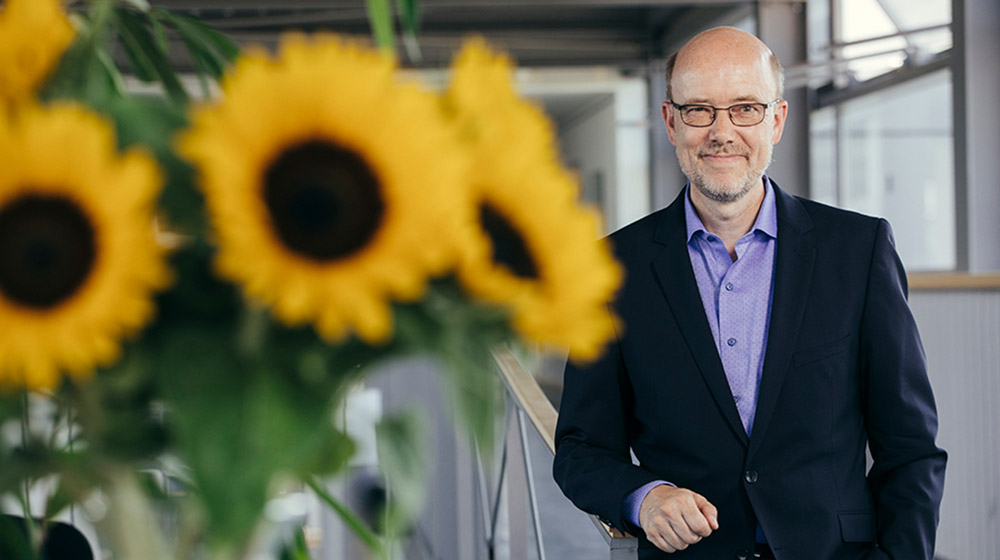
Wer würde ausgerechnet die chemische Industrie mit Öko, Grün und Bio in Verbindung bringen? Sie steht in den Köpfen vieler Menschen doch eher für Umweltverschmutzung; sie verpestet mit hochgiftigen Substanzen die Flüsse und die Luft und verbraucht noch dazu Unmengen an Energie. Erneuerbare Energien, nachhaltige Rohstoffe, Recycling oder Elektromobilität solche Sachen sind grüner Fortschritt. Doch obwohl die Chemieindustrie keinen besonders guten Ruf hat ohne sie geht heute gar nichts mehr. In jedem Produkt steckt irgendwie Chemie und kaum jemand möchte auf die netten Annehmlichkeiten verzichten, die Kunststoffe, Waschmittel oder Kosmetika bringen.
Wie funktioniert Grüne Chemie?
Doch wie ist die Öko-Bilanz der chemischen Industrie zu verbessern? Verfahrenstechniker der Otto-von-Guericke-Universität Magdeburg sind auf der Suche nach Alternativen, chemische Produkte nachhaltiger herzustellen. Sie arbeiten in dem von der Deutschen Forschungsgemeinschaft (DFG) geförderten Sonderforschungsbereich SFB / TRR 63 „InPROMPT: Integrierte chemische Prozesse in flüssigen Mehrphasensystemen“ daran, die Chemiebranche grüner zu machen und sie wollen Wege finden, das für viele chemische Produkte bisher als Ausgangsstoff verwendete Erdöl durch biobasierte Substanzen zu ersetzen. Gemeinsam mit Kollegen aus Berlin und Dortmund suchen sie nach neuartigen hocheffizienten Produktionsverfahren, wichtige Grundstoffe für Farben, Klebstoffe oder Waschmittel, für Spezialchemikalien oder auch für Pharmaprodukte aus nachwachsenden Rohstoffen herzustellen. „Die meisten chemischen Produktionsprozesse basieren heute noch immer auf petrochemischen Verfahren und nutzen dabei Erdöl, welches langfristig zunehmend knapper und damit teurer werden wird und dessen Verwendung die Umwelt belastet“, erläutert Professor Kai Sundmacher vom Institut für Verfahrenstechnik der Universität Magdeburg. Er ist Koordinator der Magdeburger Teilprojekte des SFB / TRR 63. „Wir möchten anstelle von Erdöl nun langkettige Kohlenwasserstoffe einsetzen, die aus Pflanzen zum Beispiel aus dem Öl von Sonnenblumen gewonnen werden können.“
„Grüne Chemie“ ist das Stichwort. Sie zielt auf eine möglichst umweltverträgliche Herstellung chemischer Produkte. Dabei nutzt sie erneuerbare Rohstoffe, setzt hoch selektiv wirkende Katalysatoren ein, verwendet unbedenkliche Lösungsmittel, achtet auf Energieeffizienz und optimiert den gesamten Produktionsprozess. Das ist auch der Ansatz des SFB / TRR 63.
Die Doktoranden Steffen Linke, Michael Jokiel und Karsten Rätze entwickeln gemeinsam neue verfahrenstechnische Prozesskonzepte. (Foto: Harald Krieg / Uni Magdeburg)
Über 60 Wissenschaftlerinnen und Wissenschaftler arbeiten seit 2010 inzwischen in der 3. Förderperiode an neuartigen „grünen“ Prozessen, für deren Realisierung sie alle Ebenen - von den molekularen Elementarschritten bis hin zum Betrieb der Gesamtanlage ganzheitlich betrachten. „Langfristig möchten wir eine Methodik entwickeln, mit der auf Basis von Computersimulationen die optimale Prozesskonfiguration, die intelligenteste Betriebsführung und das beste Lösungsmittel vorausberechnet werden können. Zudem soll durch genaue Planung von Schlüsselexperimenten der größtmögliche Informationsgewinn erzielt und damit die Prozessentwicklung stark beschleunigt werden“, unterstreicht Professor Sundmacher.
Aktuelle Forschungsergebnisse fließen kontinuierlich in die Lehrkonzepte ein. Jeder Lehrende sollte seine Lehrangebote immer wieder auf den Prüfstand stellen und anpassen. Die Evaluierungssysteme an der Uni seien dabei sehr hilfreich, betont Professor Sundmacher. „Das ist oft anstrengend, aber lohnend, denn die Universität bildet nicht nur wissenschaftlichen Nachwuchs aus, sondern vor allem Ingenieure für die Industrie. Von uns ausgerüstet mit einem hohen Maß an Selbstständigkeit und Lösungskompetenz nehmen die Absolventen neueste wissenschaftliche Erkenntnisse und das Bewusstsein für die Notwendigkeit einer nachhaltigen Chemieproduktion mit an ihren Arbeitsplatz.“
Die Nachhaltigkeit als neue Herausforderung
Nachdem es in den vergangenen acht Jahren den Wissenschaftlern gelungen ist, drei innovative Phasensysteme das sind die Umgebungen, in denen die chemischen Reaktionen ablaufen für biobasierte Rohstoffe zu entwickeln, geht es jetzt darum, ihre Verwertbarkeit zu überprüfen. Das geschieht in sogenannten Miniplants, d. h. in Modellanlagen, welche die später eingesetzten Großanlagen im Kleinen nachbilden. Damit können Vorgänge realistisch nachvollzogen und technische Veränderungen in der Arbeitsweise simuliert werden. Eine Miniplant, in der die Veränderungen von Prozessparametern, wie das Mischungsverhältnis von Ausgangsstoffen, Katalysator und Lösungsmittel, oder auch der Einfluss der Temperatur erkundet werden, steht im Technikum des Magdeburger Max-Planck-Instituts für Dynamik komplexer technischer Systeme (MPI). Diese Anlagen en miniature machen es möglich, den Ablauf der chemischen Reaktion, die Stabilität des homogenen Katalysators und die Effizienz der eingesetzten Lösungsmittelsysteme realitätsnah zu bewerten.
Um Umwandlungsprozesse in der grünen Chemie effizient durchzuführen, werden spezielle, sogenannte homogene Katalysatoren eingesetzt. Diese Katalysatoren schwimmen im Reaktionsgemisch und können jedes Rohstoffmolekül zielgerichtet in das gewünschte Produktmolekül umbauen. Allerdings müssen die Katalysatoren nach ihrem Einsatz vom Produkt getrennt und wiederverwendet werden. Dieses Recycling ist eine große Herausforderung, aber aus ökonomischen Gründen notwendig. Homogene Katalysatoren sind oft fragil, werden bei zu hohen Temperaturen rasch zerstört; vor allem aber sind sie, wie z. B. das häufig verwendete Edelmetall Rhodium, sehr teuer. Gelingen kann die Trennung, indem sogenannte „schaltbare“ Lösungsmittel verwendet werden. Bei hoher Temperatur liegt nur eine flüssige Phase vor, in der sich die Reaktionspartner ideal vermischen können. Nach Abkühlung entstehen aber zwei flüssige Phasen: eine polare und eine unpolare Phase vergleichbar mit Wasser und Öl, die sich nicht vermischen. In der unpolaren flüssigen Phase reichert sich das Zielprodukt an, in der anderen Phase der Katalysator, der dann wieder für die Reaktion verwendet werden kann. Bei der Suche nach dem optimalen Lösungsmittel, das man in einem bestimmten Temperaturbereich zwischen einer und zwei Phasen hin- und herschalten kann, kommt auch die Quantenchemie zum Einsatz. Mit ihrer Hilfe kann der Ablauf der chemischen Reaktion am Katalysator in verschiedenen Lösungsmitteln in allen molekularen Details im Computer simuliert werden.
Unter Druck werden flüssige und gasförmige Substanzen in einem Rührkessel zur Reaktion gebracht. Die entstehendn Produkte werden mit einer optischen Sonde gemessen. (Foto: Harald Krieg / Uni Magdeburg)
Neuartige Phasensysteme, auf die sich die Aufmerksamkeit der Forscher richtet, sind thermo-morphe (TMS) und mizellare (MLS) Lösungsmittel sowie Pickering-Emulsionen. Trotz ihrer hervorragenden Eigenschaften werden sie großtechnisch bisher kaum genutzt. Der Stoffaustausch an der Grenzfläche zwischen den flüssigen Phasen ist in diesen Systemen recht komplex und nicht vollständig verstanden. Daher wird momentan am Institut für Apparate und Umwelttechnik ein Modellapparat entwickelt, um den Stofftransport über Grenzflächen hinweg aufzuklären. Für die strömungsmechanische Optimierung neu entwickelter Apparate werden zudem die Strömungsphänomene in den flüssigen Mehrphasensystemen, insbesondere das Vermischungs- und Entmischungsverhalten, am Institut für Strömungstechnik und Thermodynamik genauer unter die Lupe genommen.
Wann setzt sich das Bio-Label in der Chemie durch?
„Ein sehr wichtiger Gesichtspunkt wird vom Endverbraucher häufig gar nicht wahrgenommen: die oft hochtoxischen Lösungsmittel, die bei chemischen Reaktionen vielfach verwendet werden“, erläutert Kai Sundmacher. Hier sieht er einen wichtigen Ansatzpunkt für eine nachhaltigere Chemieproduktion. „Es gilt, alternative Lösungsmittelsysteme ohne negative Auswirkungen auf Gesundheit und Umwelt zu finden und großtechnisch einzusetzen. Die Lösungsmittelbelastung von Produkten muss so gering wie möglich sein, da der Verbraucher später körperlichen Kontakt mit den Produkten hat oder diese in seinem Wohnraum nutzt.“
Das umweltfreundlichste Lösungsmittel ist Wasser, aber dieses ist leider als Trägersubstanz in chemischen Prozessen nur in den seltensten Fällen geeignet. Um nun die Eigenschaften alternativer Lösungsmittel möglichst umweltfreundlich zu gestalten, wollen die Wissenschaftler direkt in das Design des Moleküls eingreifen. „Ähnlich wie beim LEGO wollen wir Lösungsmittel aus molekularen Baugruppen zusammensetzen und dabei gezielt optimieren“, ergänzt Professor Sundmacher. „Bisher wurde diese Aufgabe weitgehend empirisch, also aus Erfahrung und Beobachtung heraus, gelöst. Zukünftig werden wir dafür gemeinsam mit Professor Achim Kienle vom Institut für Automatisierungstechnik leistungsfähige Methoden der mathematischen Optimierung nutzen. Unsere Vision ist es, die besten Produktionsprozesse und die besten Lösungsmittelmoleküle in einem Zug gleichzeitig zu ermitteln. Wir sind überzeugt, dass sich damit neue verfahrenstechnische Produktionsprozesse entwickeln lassen, die die heutigen in Bezug auf Effizienz und Nachhaltigkeit bei weitem übertreffen werden.“ Um Abfallstoffe zu vermeiden und den Energiebedarf zu reduzieren, werden nicht nur die erwünschten chemischen Hauptreaktionen, sondern auch alle Begleitreaktionen untersucht. Reaktionsnetzwerke funktionieren quasi wie komplexe Verkehrssysteme. Werden die Geschwindigkeit und der Zustrom der Verkehrsteilnehmer nicht gesteuert, ist die Kreuzung irgendwann unweigerlich verstopft. Genauso ist es mit den Abläufen in einem chemischen Reaktor. Wann wieviel wovon in den Reaktor eingebracht wird, ist entscheidend für den Verlauf der Reaktion und die Vermeidung von Abfallstoffen.
Der Weg von einer immer noch stark erdölbasierten hin zu einer biobasierten chemischen Industrie sei noch recht weit, schätzt Professor Kai Sundmacher ein. Noch seien fossile Rohstoffe relativ kostengünstig zu erhalten und noch sei der Verbraucher nicht bereit, für ein Bio-Label in der Chemie wesentlich mehr zu bezahlen. Aber der Wissenschaftler ist zuversichtlich: „Mit den Bio-Eiern hat das auch ein Weilchen gedauert. Die Verbraucher und Verbraucherinnen steuern den Erfolg der grünen Chemie mit ihrem Kaufverhalten. Langfristig wird sich das durchsetzen. Der globale Trend weg von den fossilen Rohstoffen ist bereits deutlich erkennbar.“ Für Sachsen-Anhalt sieht Kai Sundmacher großes Potenzial in der grünen Chemie, und das nicht nur wegen des bekannten Chemiedreiecks mit langer Tradition im Süden des Bundeslandes. In Sachsen-Anhalt könne chemische Industrie und landwirtschaftliche Produktion zukünftig in einer nachhaltigen Produktionsstruktur enger gekoppelt werden. Sektorenkopplung wird das genannt, wenn produzierende Branchen, die zunächst wenig miteinander kooperiert haben, zusammengebracht werden. Noch existiert kein integriertes System von chemisch-pharmazeutischer Produktion im Raum Halle, Merseburg, Bitterfeld und landwirtschaftlicher Produktion in Altmark und Börde. Es verlange neue systemische Ansätze, den gesamten Kreislauf vom Rohstoff zum Produkt und über Recycling wieder zurück zu den Rohstoffen zu betrachten, dabei ökonomische und ökologische Faktoren in die Analyse einzubeziehen und zielgerichtet disruptive Technologien einzusetzen.
Kai Sundmacher über seine Arbeit als Wissenschaftler
„Mich begeistert das Humboldtsche Prinzip der Einheit von Forschung und Lehre. Es sollte unbedingt der Leitgedanke für die deutsche Universitätslandschaft bleiben. An kreativer wissenschaftlicher Arbeit in der anwendungsorientierten Grundlagenforschung, wie sie an der Otto-von-Guericke-Universität Magdeburg und dem Max-Planck-Institut für Dynamik komplexer technischer Systeme in Magdeburg möglich ist, habe ich besonders Freude. Mit vielen Freiheiten, neue Ideen in die unterschiedlichsten Richtungen denken zu dürfen, kann ich an der Fakultät für Verfahrens- und Systemtechnik ergebnisoffen forschen.“