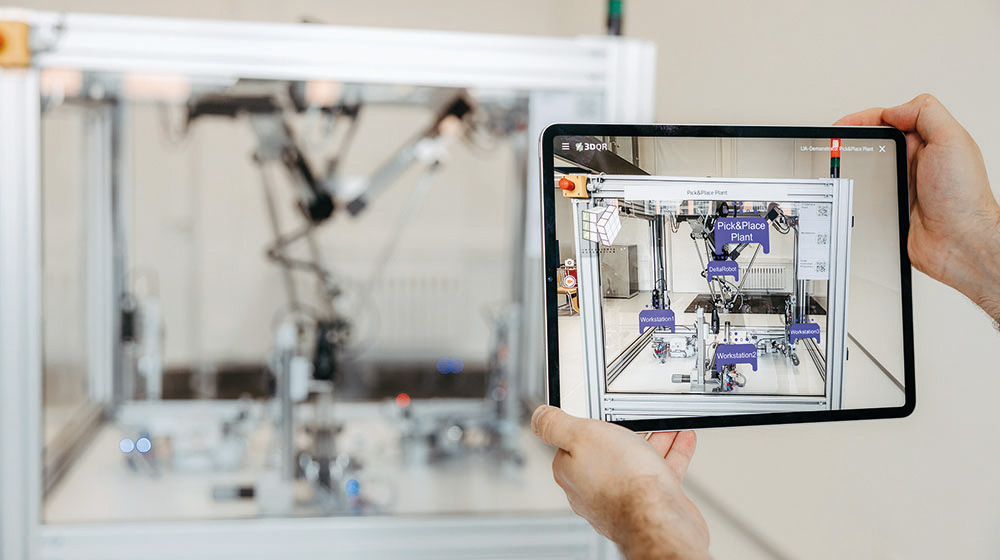
Einst wollte das babylonische Volk einen Turm hoch in den Himmel bauen, um mit Gott auf Augenhöhe zu stehen. Doch Gott stiftete eine Sprachverwirrung, um dieses Vorhaben zu vereiteln. Verständigungsschwierigkeiten ließen das Vorhaben zu keinem glücklichen Ende führen. Seitdem leben die Menschen mit unterschiedlichen Sprachen in der ganzen Welt verstreut – so erzählt es die Geschichte vom Turmbau zu Babel. Das „babylonische Sprachgewirr“ hat sich als Redewendung bis heute erhalten. Die Menschen haben – weil sie intelligent sind – Möglichkeiten gefunden, sich weltweit zu verständigen; trotz ihrer Sprachbarrieren.
In ihrem ungebremsten Forscherdrang wollen sie längst auch ihren Maschinen beibringen, auf intelligente Art und Weise miteinander zu kommunizieren und zu arbeiten. Im digitalen Zeitalter eröffnen sich da ganz neue Möglichkeiten. Allerdings würde auch hier ein „babylonisches Sprachgewirr“ zu Problemen führen. „Es leuchtet ein, dass für die Verständigung der Maschinen untereinander eine genaue und eindeutige Sprache wichtig ist“, meint Christian Diedrich, Leiter des Lehrstuhls Integrierte Automation an der Fakultät für Elektrotechnik und Informationstechnik der Otto-von-Guericke-Universität Magdeburg. Die Uni teilt ihre Vision von smarten Wertschöpfungsketten mit dem Verband Deutscher Maschinen- und Anlagenbau und mit dem Verband der Elektro- und Digitalindustrie. Gemeinsam mit Firmen aus dem Maschinenbau, der Elektroindustrie und aus der Softwarebranche arbeitet die Gruppe um Christian Diedrich in der 2021 gegründeten „Industrial Digital Twin Association“.
Prof. Dr.-Ing. Christian Diedrich (Foto: Jana Dünnhaupt / Uni Magdeburg)
„Die Kommunikation von Komponenten und ganzen Industrieanlagen soll über deren digitale Zwillinge geführt werden“, sagt Christian Diedrich. Er leitet das Industrial Digital Twin Projekt an der Magdeburger Uni. Dessen Kernaufgabe ist es, die Interoperabilität, also die Zusammenarbeit zwischen verschiedenen digitalen Zwillingen, weltweit zu ermöglichen. „Wir beteiligen uns an der Entwicklung von technischen Normen, von gemeinsamen Standards, an die sich die IT-Systeme halten müssen“, sagt der Professor für Integrierte Automation. Diedrich rühmt die Maschinenbauleistung „made in Germany“: „Maschinen aus Deutschland haben nach wie vor einen sehr guten Ruf auf dem Weltmarkt.“ So ist denn auch der traditionsreiche Maschinenbau immer noch die größte Fachdisziplin an der Magdeburger Uni.
Das technische Denkmal einer Dampfmaschine auf dem Uni-Campus erinnert an die erste industrielle Revolution. Über die Einführung der Elektrizität (2.0) und die Nutzung von Elektronik und IT (3.0) mündet der Wandel der Industrie nun in die industrielle Revolution 4.0 – gekennzeichnet von intelligenten, sich selbst organisierenden Anlagen und Maschinen. Auch auf diesen Fachgebieten hat sich die Universität Magdeburg einen exzellenten Ruf erworben. „Wenn unsere Maschinen künftig Komponenten von intelligenten, autonomen, sich selbst organisierenden Wertschöpfungsketten sein sollen, dann müssen wir sie in diesen technologischen Leistungsstand versetzen. Und wir können das“, ist der Experte überzeugt. Denn die Automatisierungstechnik verbinde die maschinenbaulichen, elektrotechnischen und informationstechnischen Kompetenzen an der Magdeburger Uni.
Die Bearbeitungsstation wird mittels I4.0 Sprache mit Aufträgen versorgt (Foto: Jana Dünnhaupt / Uni Magdeburg)
Die Universität Magdeburg gehört zu den Vertretern aus Wirtschaft, Wissenschaft und Politik, die sich auf der Plattform Industrie 4.0 zusammengeschlossen haben, um die digitale Transformation der Produktion in Deutschland voranzubringen und die Wettbewerbsfähigkeit des Produktionsstandortes zu stärken. Arbeitsgruppen wollen wichtige Zukunftsfragen beantworten – so auch die der Systemarchitektur, der Modelle und Standards. „Wir entwickeln die Grundlagen für offene Standards, die für die Anwender- wie auch Anbieterbranchen für Hard- und Software geltend sind“, sagt Christian Diedrich. Klar: Die besagte babylonische Sprachverwirrung wäre auch von intelligenten Maschinen nicht beherrschbar. Gerade innerhalb eines Wertschöpfungsprozesses ist es wichtig, dass Informationen exakt und in Echtzeit verstanden werden.
Christian Diedrich und seine wissenschaftlichen Mitarbeiter Chris Urban, Alexander Belyaev und Harish Pakala zeigen an einem Demonstrator für smarte auftragsgesteuerte Produktion, wie die physische und die virtuelle Welt zusammenwachsen. Deutschlandweit haben hier Entwickler die Möglichkeit, ihre digitalen Zwillinge à la Plattform Industrie 4.0, auch als Verwaltungsschale bezeichnet, zusammenzuschalten und zu erproben, wie sie sich miteinander vernetzen – von der automatisierten Auftragsplanung und Auftragsvergabe bis zur autonomen Produktionssteuerung. Wenn in diesem Prozess ein Fehler aufträte, würden die Verwaltungsschalen selbstständig nach Alternativen suchen, damit die Produktion nicht angehalten werden muss. Die Miniatur-Anlage, die völlig autonom aus einem Metall-Rohling einen Zylinder herstellt, erzielte schon große Aufmerksamkeit auf Messen und Kongressen.
Alexander Belyaev bedient über eine AR-App die Anlage (Foto: Jana Dünnhaupt / Uni Magdeburg)
Chris Urban scannt QR-Codes ein, mit denen jedes der realen Teile der Anlage, die Assets, gekennzeichnet sind. „Hinter jedem QR-Code steckt ein virtuelles Abbild des realen Teils, ein digitaler Zwilling“, erklärt Urban. Er hat Mechatronik studiert und ist an Entwicklung und Optimierung dieses deutschlandweiten Demonstrators beteiligt. Nach seinen Erläuterungen kann man sich die Verwaltungsschalen tatsächlich wie Aufbewahrungsboxen vorstellen, die viele wichtige Informationen zum jeweils real existierenden Maschinenteil bekommen und diese dann verwalten. Der digitale Zwilling des Produktes „Zylinder“ zum Beispiel kennt die Fertigungsschritte und die Anforderungen, die mit diesem Produktionsprozess zusammenhängen. Völlig autonom initiiert er die nötigen Bearbeitungsprozesse wie Bohren und Schleifen, weil er sich mit den digitalen Zwillingen der dafür notwendigen Werkzeuge verständigen kann. „Jedes Nachrichtenelement besitzt eine Identifikationsnummer und ist somit für die Maschinen verständlich“, sagt Alexander Belyaev. Er hat an der Magdeburger Uni Elektrotechnik und Informationstechnik studiert und forscht an der Semantik der digitalen Zwillinge; also an den sprachlichen Zeichen, die auf der ganzen Welt eine einheitliche Bedeutung haben, beziehungsweise bekommen sollen. „Wir entwickeln das Konzept für ein digitales Lexikon, in dem unter Sachgebieten geordnet steht, was die IDs bedeuten“, sagt Belyaev.
Chris Urban zeigt Details der I4.0-Sprache bei der Interaktion zwischen den Maschinen (Foto: Jana Dünnhaupt / Uni Magdeburg)
Auf dem Tablet von Chris Urban ist unterdessen dokumentiert, wie sich die für den Arbeitsprozess „Bohren“ zuständigen digitalen Zwillinge verständigt und ihre Entscheidungen ohne jegliche zentrale Steuerungsinstanz getroffen haben. Wesentlich für diese Kommunikation ist die Vernetzung der digitalen Zwillinge im „Internet der Dinge“, wo sie Daten austauschen etwa über Fähigkeiten, Eigenschaften und Zustände der realen Komponenten; so zum Beispiel über die Materialbeschaffenheit des Rohlings, aus dem ein Zylinder werden soll und über die Anforderungen, die an das Produkt gestellt werden. Aus dem Protokoll ist aber auch ablesbar, was die Verwaltungsschalen noch „verwalten“ können. Sie suchen über Unternehmensgrenzen hinweg nach Maschinen und Produktionsstandorten, die das Produkt nach definierten Parametern in einer bestimmten Zeit- und Preisspanne herstellen können. Sie binden Fähigkeiten und freie Kapazitäten anderer Firmen in die eigene Produktion ein und erweitern somit das eigene Spektrum. Sie prüfen gleichsam Möglichkeiten, eigene freie Produktionskapazitäten auf dem Markt anzubieten, um so eine höhere Auslastung der Maschinen zu erreichen. Ziel solcher intelligenten Prozessketten ist eine effizientere und Ressourcen schonende Produktion. Neu ist in diesem Zusammenhang der Begriff „Industrie 4.0-Ökosystem“.
Harish Pakala zeigt den von ihm entwickelten Digitalen Zwilling (Foto: Jana Dünnhaupt / Uni Magdeburg)
Damit Forschung und Entwicklung innerhalb des Industrial-Digital-Twin-Projektes nicht an den Bedürfnissen der Anwender vorbei gehen, pflegt die Uni eine enge Zusammenarbeit mit Partnern aus der Wirtschaft wie dem Maschinen- und Anlagenbauer Wittenstein oder der Technologie-Initiative SmartFactory und mit Partnern aus der Forschung wie der Rheinisch-Westfälischen Technischen Hochschule Aachen, dem Fraunhofer-Institut für industrielle Automation IOSB-INA Lemgo und dem ifak – Institut für Automation und Kommunikation Magdeburg. Ihnen allen tut sich eine ganz naheliegende Frage auf: Wo sollen diese vielen Informationen verarbeitet werden? Projektleiter Diedrich verweist auf ein real-praktisches Beispiel der Verständigung und Zusammenarbeit von Automatisierungs- und IT-Experten, aus der eine echte Innovation hervorgeht: „Die Datenverarbeitung soll so weit wie möglich direkt in die Anlagen integriert werden. Diese Lösung verkleinert sogar den CO2-Fußabdruck dieser intelligenten Maschinen.“
GUERICKE facts
- Ein „Digitaler Zwilling“ ist ein Daten- und Softwareabbild von Maschinen und Anlagen. Er stellt Informationen über Konstruktion, Inbetriebnahme, den operativen Betrieb bis hin zur Verschrottung bereit.
- Durch Clouds, Internet of Things oder Blockchain können sich Maschinen, Anlagen und ganze Smarte Fabriken vernetzen. Dafür müssen alle Daten maschinell lesbar sein und sich Maschinen untereinander mittels eindeutiger Sprache verstehen können.
- Die I40-Sprache definiert analog zu einer menschlichen Sprache Regeln für Vokabular, Sätze und Dialoge.